
LASER WELDING PLASTIC
The laser offers optimal joining technologies - not only for bonding metals, but also plastics. The advantages are obvious: clean and narrow weld seams, a very minimal heat-affected zone and maximum flexibility - ideal prerequisites for processing high-quality plastic components, for example.
Each application poses its own set of challenges. Based on our broad portfolio of laser welding systems, we objectively design the most innovative and best solution for our customers.
Our laser welding stations can be individually upgraded with various additional components and meet the highest demands of flexibility, user-friendly operation and reliable process monitoring.
OUR SERIES
Our advanced systems enable you to perform high-precision laser welding at the highest level. You can rely on our know-how and our technical experience - we will be happy to advise you.
INTEGRAL SOLUTION
We offer you laser systems that you can easily integrate into your existing systems and machines - for all applications.
COMPACT PLATFORM
Our standard laser systems for cutting, labeling and welding components. The systems are designed so flexibly that they can be used for many applications and products.
SELECT PLATFORM
All systems of the SELECT series are configured individually and tailor-made for your application.
BENEFITS OF
LASER WELDING PLASTIC
We offer you solutions for all possible process variants and materials. Both transparent-absorbing joints and transparent-transparent combinations can be firmly bonded together. This works with or without absorber application when using medium IR wavelengths. We offer you solutions for contour, quasi simultaneous or simultaneous laser transmission welding.
Laser transmission welding of plastics achieves higher strengths compared to other welding processes such as ultrasonic, friction, heating element or hot gas welding. Weld seams achieve maximum tensile/shear strength by substance-to-substance joining, i.e. chemical interlinking of transparent and absorbing joining partners. As a result, the basic material strength is achieved, i.e. the joining partners more or less behave like a "single-cast injection moulding" component.
​
This can only be achieved by locally limited, precise & homogeneous energy supply across the weld seam width (process-optimised power density distribution).
The results are pore-free, spatter-free and absolutely particle-free welding processes, a basic requirement e.g. for electronic/sensor technology/medical products.
MORE LASER PROCESSES
Are you interested in other laser processes?
If you have any questions about specific processes or automation solutions, please do not hesitate to contact us.

CONTUR WELDING
With this process control, a laser spot is passed once over the welding contour of the component. The following basic solutions are possible:
1.1) A fixed spot optic is guided over the component in order to connect the joining partners with 2 or 3D geometry. The size of the component is unlimited.
1.2) A scanner system directs the laser spot over the welding contour of the component in order to connect the joining partners with 2 or 3D geometry. The component must not be larger than the scan field.
1.3) Hybrid contour welding with a scanner system that is moved over the component by a guide axis system. The scanner mirror movement takes place synchronously with the axis movements of the linear axes in order to cover larger component dimensions. The advantage here is that complex, filigree contour elements are dynamically welded using the scanner system, while simple, larger contours are also covered using the linear axis system. The welding speed is always constant because the scanner movement and axis movement are synchronized.


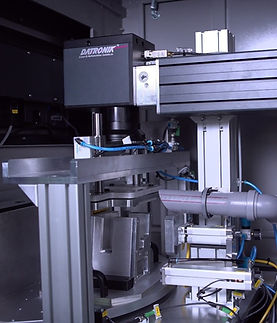
QUASI-SIMULTANEOUS WELDING
2.1) A scanner system steers the laser spot with rel. high speed several times over the welding contour of the component in order to connect the joining partners with 2 or 3D geometry. The component must not be larger than the scan field.
2.2) Hybrid quasi-simultaneous welding with a scanner system that is moved over the component by a guide axis system. The scanner mirror movement takes place synchronously with the axis movements of the linear axes in order to cover larger component dimensions. The advantage here is that even large components, beyond the scan field size, can be welded quasi-simultaneously in sections. This allows e.g. location-dependent temperature zones in the component achieve.
3) SWEEP WELDING
A scanner system controls the rel. small laser spot at very high speed on a wobble geometry that can be programmed in a highly variable manner depending on the process. In this way, a time-changeable "energy profile" is achieved on the welding contour of the component. The width of the weld seam can also be adjusted very flexibly via the wobble radius.
This type of process control can be carried out both in classic laser transmission welding with a transparent and absorbent joining partner and in the welding of transparent "clear-clear connections" with a wavelength of approx. 2 µm.


OTHER VARIANTS
SIMULTANEOUS WELDING
The component is simultaneously welded with a fixed laser beam geometry, with a defined intensity profile, i.e. the entire welding contour is welded using the appropriate laser light distribution, without moving the component or the laser spot. Examples are rotationally symmetrical ring distributions from outside or inside or line distributions.
MASK WELDING
The welding contour is defined using a welding mask, which is scanned over the component and scanned with a linear laser light distribution. Alternatively, the welding mask can be exposed simultaneously with a flat laser light distribution in order to achieve even shorter cycle times. The corresponding light distributions can be set using static laser light distributions or high-speed scanners.
MATERIAL COMBINATIONS
TRANSPARENT – ABSORBEND
There is a laser-transparent and a laser-absorbent joining partner. The laser-transparent, upper joining partner is Process variants irradiated and cohesively connected via the absorption in the lower, absorbent joining partner. The required joining pressure ensures the form fit between the joining partners before welding.
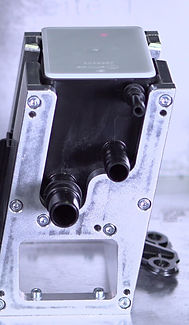

VISUAL BLACK / LASERTRANSPARENT – ABSORBEND
See above, with the difference that the upper joining partner appears visually and optically black.
TRANSPARENT – TRANSPARENT
Both joining partners are laser-transparent, i.e. the interaction between laser radiation and plastic must be achieved via an additional absorber medium or via an alternative laser wavelength.


WITH NIR ABSORBER LIQUID
The laser welding between the two joining partners takes place in two process steps. An absorber liquid that dries quickly is first applied to the lower joining partner. This means that this process step can also be carried out “inline” with a short drying waiting time. Alternatively, the absorber liquid can be applied in advance and the components can then be stored. The absorber is not subject to any aging effects.
Datronik is the official distributor for the absorber liquid with the brand name "Clearweld" from the U.S. company Crysta-Lyn Inc. (http://www.clearweld.com). This absorber has the advantage that it appears colorless after the laser welding process and thus crystal-clear joint connections in components e.g. made of polycarbonate.
Due to the exact controllability of the absorption rate via the amount of absorber liquid and the type of application, variable interactions can be achieved between the joining partners, which offer technological advantages. For example, "Sandwich welds" with 2 superimposed butt joints possible in one welding process by precisely dividing the laser power into the upper and lower butt joints.
This will e.g. tight welds on round outer contours possible without having to move the entire component from the outside. Datronik supplies the complete technology package, including a process-reliable and precisely metered absorber application system and fluid delivery from the liquid tank.
WITH "MIR" WAVELENGTH
(APPROX. 2 µm)
As an alternative to the absorber application, suitable laser types can be used with 2 laser-transparent joining partners, even without an absorber. For this, a wavelength must be used that radiates through the upper joining partner, but is absorbed in the lower joining partner. The interaction between laser radiation and plastic only takes place in the interface area between the joining partners.
Datronik has developed suitable process variants and parameters in several practical examples. In close cooperation with the customers, the components were designed with suitable joining geometries. Practical examples are microfluidic components in the medical industry and liquid-carrying components in energy storage technology.
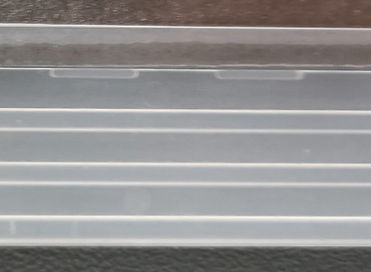
PROCESS MONITORING, ASSURANCE AND DOCUMENTATION
1) FORCE-DISPLACEMENT MEASUREMENT AND MONITORING DURING SIMULTANEOUS / QUASI-SIMULTANEOUS WELDING
With simultaneous or quasi-simultaneous laser transmission welding, the entire component welding contour is melted over the width of the weld seam at the same time, causing the upper joining partner to sink onto the lower joining partner. This joining path can be measured precisely in the device and is a measure of the resulting melt volume or the lateral melt expulsion. Depending on the component tolerances, a minimum dimension of the joining path is defined, which maximizes the process reliability for the tight welding of the component. The achievement of the minimum size in a defined period is monitored. In addition, the applied joining force between the welding partners is measured, so that a missing form fit or a pressure drop in the pneumatic device is recognized.
2) TEMPERATURE MEASUREMENT CONTROL, MONITORING BY PYROMETRY OR IR CAMERA
With quasi-simultaneous or contour welding, the process temperature in the laser spot can be measured in real time without contact and at high speed during laser welding. This results in a high-resolution measuring temperature field of the welding contour. Different evaluation strategies are selected depending on the component:
​
- Process temperature monitoring during laser welding via tolerance envelopes.
​
- Process temperature control to keep the welding temperature constant regardless of the feed speed and component geometry.
​
- Measurement of spatially resolved temperature zones / fields, as well as control of the process temperature spatially and temporally.


WELD INSPECTION BY VISION SYSTEMS
4.1) Follow-up, optical weld inspection for quality assessment / control of the welding result.
4.2) Preliminary inspection of the joining zone for the seam guidance of the process tool.
MORE LASER PROCESSES
Are you interested in other laser processes?
If you have any questions about specific processes or automation solutions, please do not hesitate to contact us.
LASER MARKING
Plastic or metal - Durable, high-contrast laser marking with great flexibility.
LASER CUTTING METAL
The laser proves to be the tool of choice, especially when cutting, separating and perforating.
LASER CUTTING PLASTIC
The laser proves to be the tool of choice, especially when cutting, separating and perforating.

LASER ABLATION
The laser makes the processing and cleaning of component surfaces simple and efficient.
LASER WELDING METAL
The laser offers optimal joining technologies - not only for bonding metals, but also plastics.